球墨铸铁件作为重要的工程材料在的很多的铸件产量中有较大的比例并且生产技术也达到了一定的水平.但由于铸造过程中的复杂性使得球墨铸铁件的质量仍然存在着很多的问题.为了更好地控制其生产质量.对出现在铸铁型材内部的夹杂缺陷,进行了地研究分析,明确了夹杂物的分布规律、元素组成、来源及形成原因,并就如何控制该缺陷的产生给出了相关的建议。对大断面型材表面出现的疤皮缺陷,分析了形成原因,讨论了影响其形成的因素,并提出了能有效疤皮缺陷的措施。优化设计后得到的铸铁型材新生产线,能够满足 尺寸为400mm的铸铁型材的生产,且生产铸铁型材的工序简化,各设备的结构组成更为简单合理.铸铁型材中的夹杂物主要聚集分布在其中心线上方约3/4半径处,其中大尺寸的夹杂物主要来源于球化和孕育处理,因此解决铸铁型材内部夹杂问题的关键是控制球化和孕育处理的相关参数. 根据生产实际及当前的关于球型石墨、晶体方面的形成、生长理论结合先进的计算机技术对金属凝固过程的观组织进行了计算机模拟仿真也称为凝固过程观模拟这个名称是相对于凝固过程宏观模拟而言的具体是指在晶粒尺度上对金属凝固过程进行模拟仿真.本文根据热力学、凝固原理等理论建立了凝固过程中热传递、溶质传递和石墨球、奥氏体的形核、生长进行模拟以能量小原理为基础考虑体积自由能和界面能的定量影响建立了晶粒生长概率模型.
亿锦天泽钢铁有限公司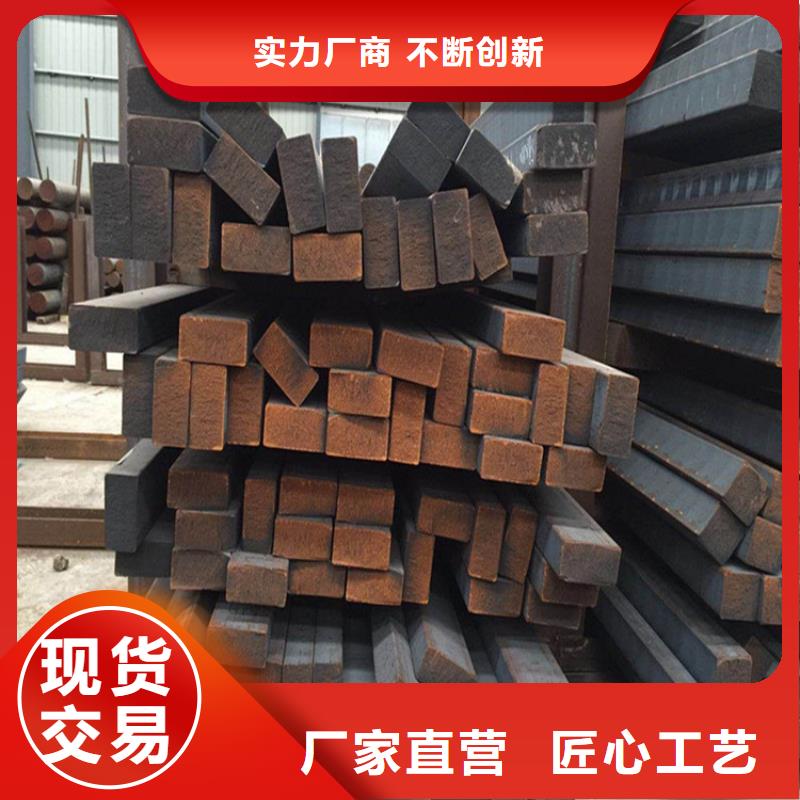
根据生产铸铁型材的技术要求采用盖包法球化处理工艺分析论述了铸态铁素体硅钼球墨铸铁制备工艺中的技术重点及难点选取化学成分、球化剂及孕育剂种类、孕育剂加入量、钼含量等参数进行试验研究有针对性地调整及优化寻求佳的制备工艺参数以稳定地生产出高性能铸态铁素体硅钼球墨铸铁。 试验采用中频感应电炉熔炼铁液铁液主要化学成分范围控制在3.3-3.5C%2.7-2.9Si%;采用快速热电偶测温控制铁液的出炉温度。通过实施反弧度法工艺,铸铁型材的鼓肚现象得到有效。但由于在率次实验过程中,刚开始生产铸铁型材时的拉拔速度比较慢、拉拔周期较长,使铸铁型材在结晶器的停留时间过长,导致在扁平方向上铸铁型材顶部略微向下凹,当拉拔参数调整合适时,下凹及鼓肚现象基本消失。反弧度法工艺制各的铸铁型材组织更为均匀,力学性能更为优良。与实施反弧度法之前的铸铁型材相比,实施反弧度法之后的铸铁型材硬度得到提高,组织更为均匀,并且其抗拉强度指标高于铸铁型材标准(JBT10854-2008水平连续铸造铸铁型材) 性能要求。同时,伸长率指标均超过LZQT500-7规定的指标。与拉伸性能结果类似,反弧度法试样的抗压强度高于未实施反弧度法试样的抗拉强度。 球化处理温度是球化处理过程中的一种重要工艺参数,球化处理温度的波动对镁的吸收率有着重要的影响。球化处理温度过高或过低,镁的吸收率都会降低,造成球化不良,球铁的综合性能和生产稳定性降低,给产品质量带来波动,增加废品率,降低综合经济效益。因此需要寻求佳的球化处理温度范围,优化盖包法工艺参数
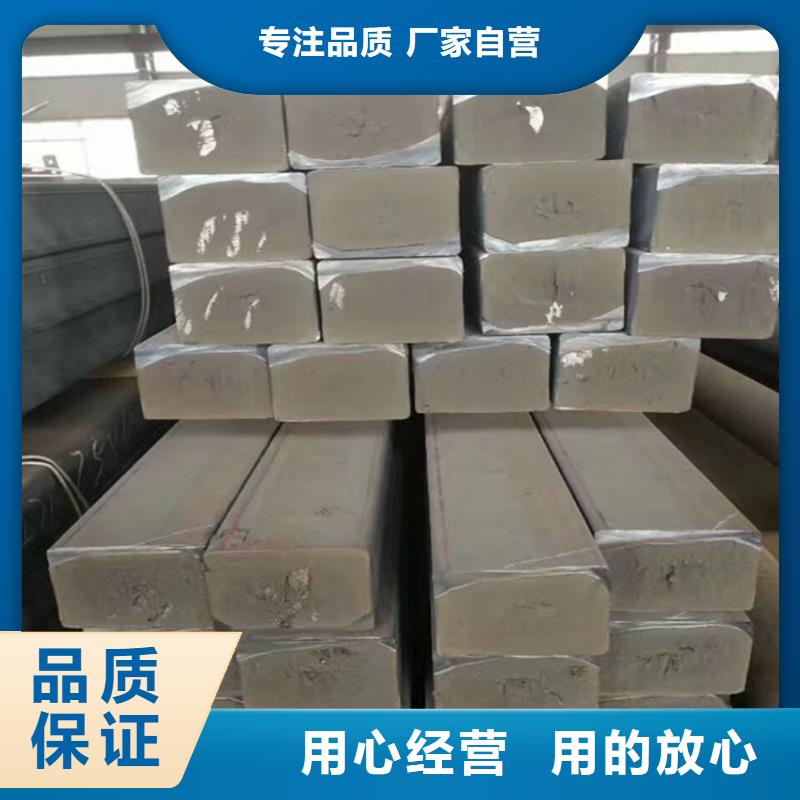
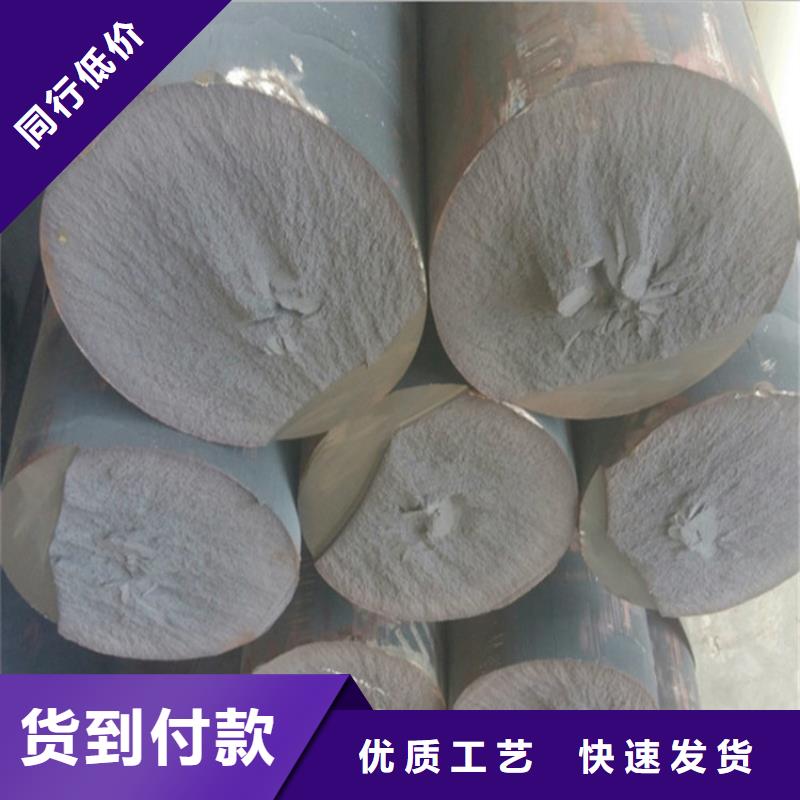