产品详情
以下是:QT400生铁棒型号齐全的产品参数
产品参数 |
---|
产品价格 | 5.6元/kg |
---|
发货期限 | 当天发货 |
---|
供货总量 | 88888 |
---|
运费说明 | 议定 |
---|
最小起订 | 5 |
---|
质量等级 | 国标 |
---|
是否厂家 | 厂家 |
---|
产品材质 | 铸铁棒 |
---|
产品品牌 | 亿锦 |
---|
产品规格 | 齐全 |
---|
发货城市 | 聊城 |
---|
产品产地 | 山东 |
---|
产品名称: | 铸铁型材 |
---|
生产工艺: | 水平连铸 |
---|
产品优势: | 无气孔/无砂眼 |
---|
产品用途: | 机械加工/精密制造 |
---|
产品价格: | 5.6元/公斤 |
导读 QT400生铁棒型号齐全_亿锦天泽钢铁有限公司,固定电话:18954456733,移动电话:0635-5083939,联系人:邢涛,QQ:1799311315,聊城开发区凤凰工业园发货到甘肃省 陇南市 武都区、成县、康县、西和县、礼县、徽县、两当县 发货到 甘肃省陇南市。 甘肃省,陇南市 陇南距今7000多年前即有人类活动,是秦人的发祥地、中国古代西部民族氐人和羌人活动的核心地区,文县白马人被誉为“东亚古老的部族”。在漫长的历史过程中,陇南既是各种政治军事力量激烈争夺的战场,又是中原中央政权与西北少数民族接触交往的前哨阵地,攻伐消长与民族交往,构成陇南社会历史的重要内容。
对灰铸铁金相图像出现的亮度不均匀现象利用空域阴影校对金相图像进行亮度不均匀校正;利用小波变换与均值滤波相结合的算法对灰铸铁金相图像进行去噪处理并取得了较好的结果。 用常用的分割算法:阈值化法、FCM聚类法、遗传算法和小波变换对灰铸铁金相图像进行分割分析了分割效果和算法的性能。同时,伸长率指标均超过LZQT500-7规定的指标。与拉伸性能结果类似,反弧度法试样的抗压强度高于未实施反弧度法试样的抗拉强度。由于铸铁型材拉坯工艺参数控制系统具有非线性和强耦合的特点,而且无法建立数学模型,采用BP、GA-BP神经网络算法进行拉坯工艺参数自适应整定研究。基于Matlab软件建立以铸造工艺参数为输入,拉坯工艺参数为输出的控制模型。仿真实验表明本文建立的拉坯工艺参数GA-BP神经网络控制模型可以用于拉坯工艺参数自适应整定,所获得拉坯工艺参数能够用于实际生产系统,实现高质量、率的铸铁型材水平连铸拉坯生产。
亿锦天泽钢铁有限公司
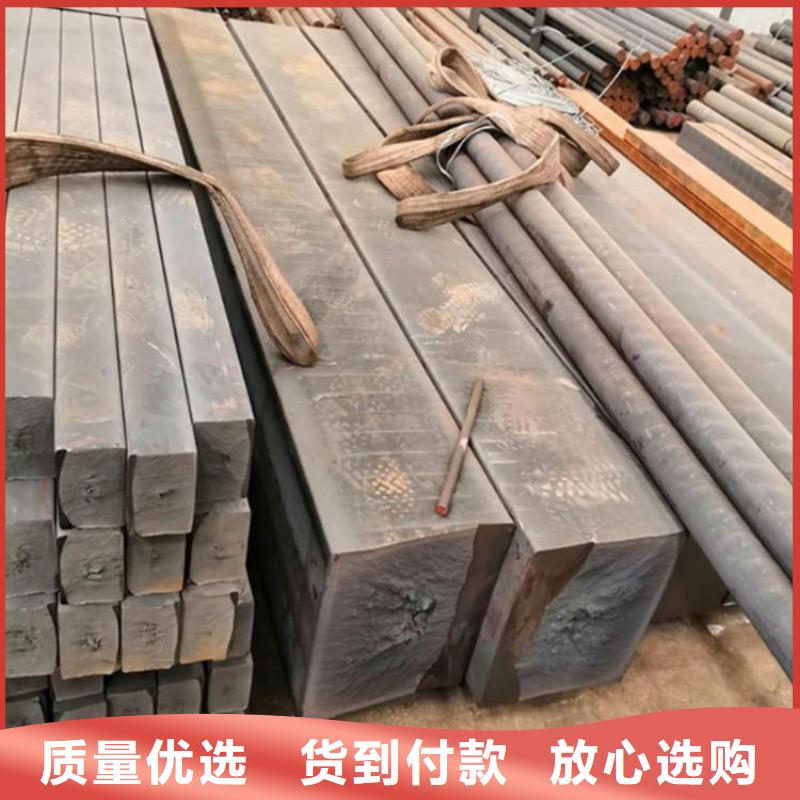
随着冷却速度的增大,石墨形态由较粗大的片状石墨逐渐变成细小的点状石墨。在厚度为30mm试样的下方放置冷铁时,在距离冷铁25mm的铸铁组织中能够获得较细小的D型石墨组织。 对不同成分的D型石墨铸铁的高温抗氧化性进行了实验研究。在750℃下,将不同成分的D型石墨铸铁保温24小时,使其氧化增重,研究成分和组织对D型石墨抗氧化性能的影响。对鼓肚缺陷,在铸铁型材的水平连铸过程中采用反弧度法工艺,即通过新型的石墨套与引锭装置来实现的,通过实施反弧度法工艺,铸铁型材的鼓肚现象得到有效。伸长率指标均超过LZQT500-7规定的指标。与拉伸性能结果类似,反弧度法试样的抗压强度高于未实施反弧度法试样的抗拉强度。
从加工性能上看来,提高Si/C比使加工性能严重恶化,随着合金化元素加入量增加,加工性能先提高后降低,在考察的孕育剂中,硅锆锰孕育剂提高加工性能和力学性能的效果也为佳。 通过分析拉伸过程以及切削加工过程中度灰铸铁的石墨变形规律,揭示出石墨对度灰铸铁抗拉强度与加工性能的影响机制。
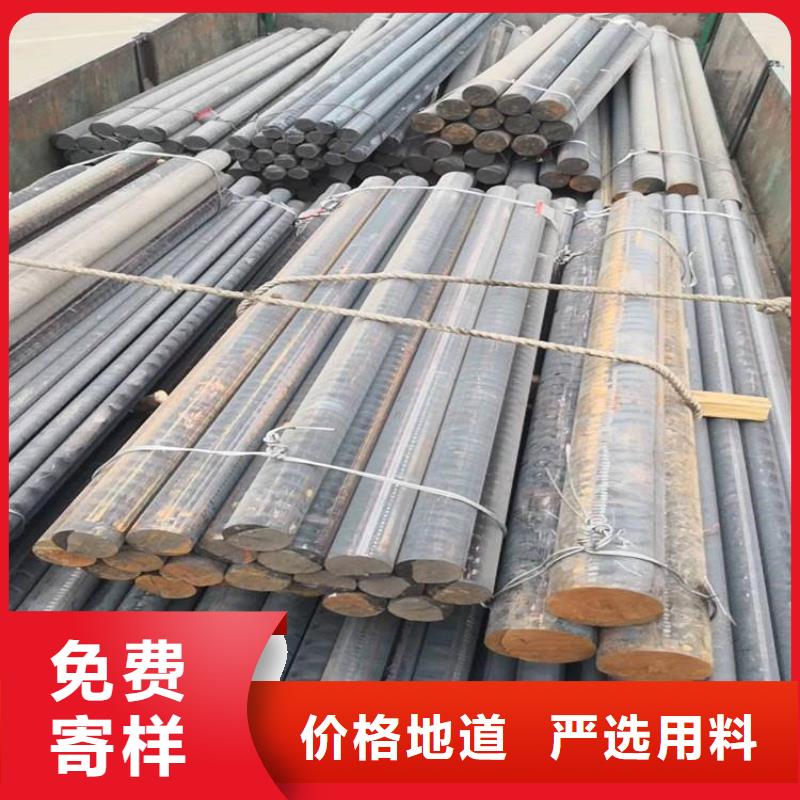
球化反应控制的关键是镁的吸收率,温度高,反应激烈,时间短,镁烧损多,球化效果差;孕育处理是球墨铸铁型材生产过程中的一个重要环节,它不仅促进石墨化,防止自由渗碳体和白口出现,而且有助于球化,并使石墨变得更细小,更圆整,分布均匀,从而提高球墨铸铁的力学性能。孕育剂一般多采用FeSi75,其加入量根据对铸件的力学性能要求,一般为0.8%~1.0%。孕育剂的粒度根据铁液量多少,一般砸成5~25mm的小块。孕育剂应保持干净、干燥。
对出现在铸铁型材内部的夹杂缺陷,进行了地研究分析,对大断面型材表面出现的疤皮缺陷,分析了形成原因,讨论了影响其形成的因素,并提出了能有效疤皮缺陷的措施。优化设计后得到的铸铁型材新生产线,能够满足 尺寸为400mm的铸铁型材的生产,且生产铸铁型材的工序简化,各设备的结构组成更为简单合理.铸铁型材中的夹杂物主要聚集分布在其中心线上方约3/4半径处,其中大尺寸的夹杂物主要来源于球化和孕育处理,因此解决铸铁型材内部夹杂问题的关键是控制球化和孕育处理的相关参数.对于铸铁型材表面存在的疤皮缺陷,生产实践证明,采取提高铁水温度、保证铁水纯净度、适当提高拉拔速度、改进炉膛底部结构及阻断结晶器两段石墨套间横向传热的举措能够有效地。
另一方面,连铸铁棒不能变截面和铸造型腔,对于一些产品的后续加工量带来很大负担。采用连续铸造工艺的球墨铸铁型材棒料和灰口铸铁棒料型材的单价为什么比砂型铸造的便宜?很多用户曾提过这个问题。因为就铸造品质而言,铸铁型材棒料没有砂眼气孔,铸造精度高,成品率几乎接近,所以价格似乎应该比翻砂件高。实际上,由于连铸型材因必须大批量生产同规格铸铁型材棒料,所以在摊平模具费用和人工费用上展现出 优势,生产成本大幅下降。
总结 在甘肃省陇南市采买QT400生铁棒型号齐全到亿锦天泽钢铁有限公司,无论您是个人用户还是企业采购,我们都将竭诚为您服务。品质保证,价格优惠,厂家直销,欢迎有需要的客户来电。联系人:邢涛-18954456733,QQ:1799311315,地址:《开发区凤凰工业园》。