以下是:铝合金型材【镀锌工角槽】研发生产销售的产品参数
产品参数 |
---|
产品价格 | 310 |
---|
发货期限 | 电议 |
---|
供货总量 | 电议 |
---|
运费说明 | 电议 |
---|
品牌 | 恒永兴 |
---|
规格 | 齐全 |
---|
价格 | 电议 |
以下是:铝合金型材【镀锌工角槽】研发生产销售的图文视频
铝合金型材【镀锌工角槽】研发生产销售,恒永兴金属材料销售
有限公司专业从事铝合金型材【镀锌工角槽】研发生产销售,联系人:李经理,电话:022-86869388、18802286588,QQ:554918566,发货地:天津北辰区双街镇京津路西(北方实业发展有限公司内)发货到湖北省 黄石市 黄石港区、西塞山区、下陆区、铁山区、阳新县、大冶市,以下是铝合金型材【镀锌工角槽】研发生产销售的详细页面。 湖北省,黄石市 黄石是中国青铜文化、矿冶文明的发祥地之一,也是近代中国民族工业的摇篮,还拥有一类水运口岸。黄石地势西南高,东北低,由西南向东北倾斜;属亚热带季风气候。2017年6月,黄石市被命名为卫生城市。2018年10月,黄石市获“森林城市”称号。
想要更直观地了解铝合金型材【镀锌工角槽】研发生产销售产品的特点和功能吗?我们为您准备了视频介绍,相较于图文,视频更能让您轻松掌握产品的核心卖点。
以下是:铝合金型材【镀锌工角槽】研发生产销售的图文介绍
恒永兴金属材料销售
有限公司有着多年 湖北黄石流体管发展历史,是一家从事 湖北黄石流体管专业设计、制造、批量生产的综合性企业。与国内多家科研院所建立密切合作关系,不断研发被用户看好的 湖北黄石流体管产品,深受广大客户好评。我公司具有完善的现代化管理模式, 湖北黄石流体管产品结构合理,性能可靠,确保向客户提供高质量的产品和周到的售后服务。

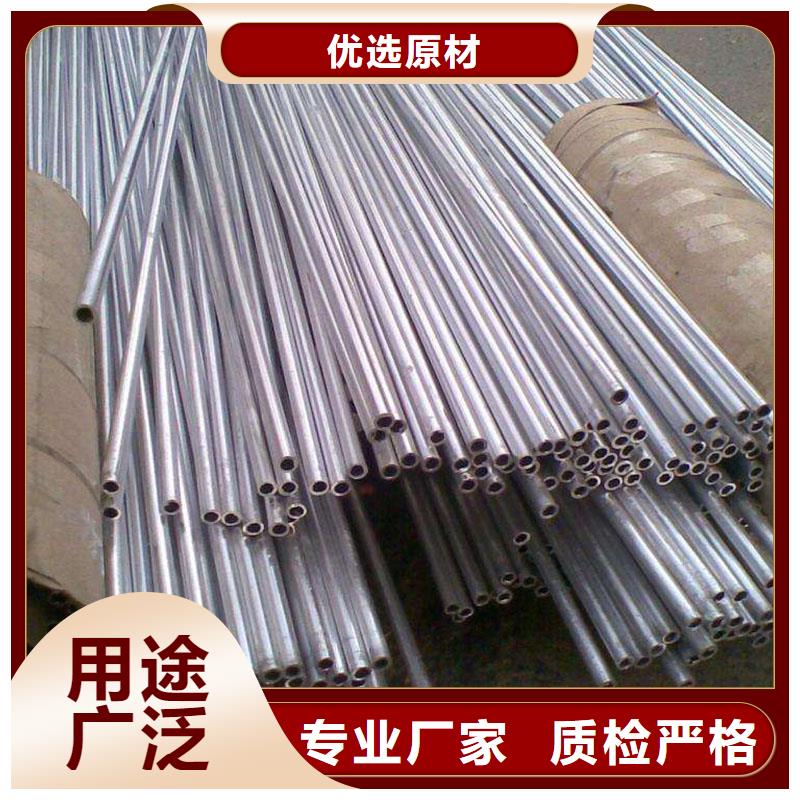
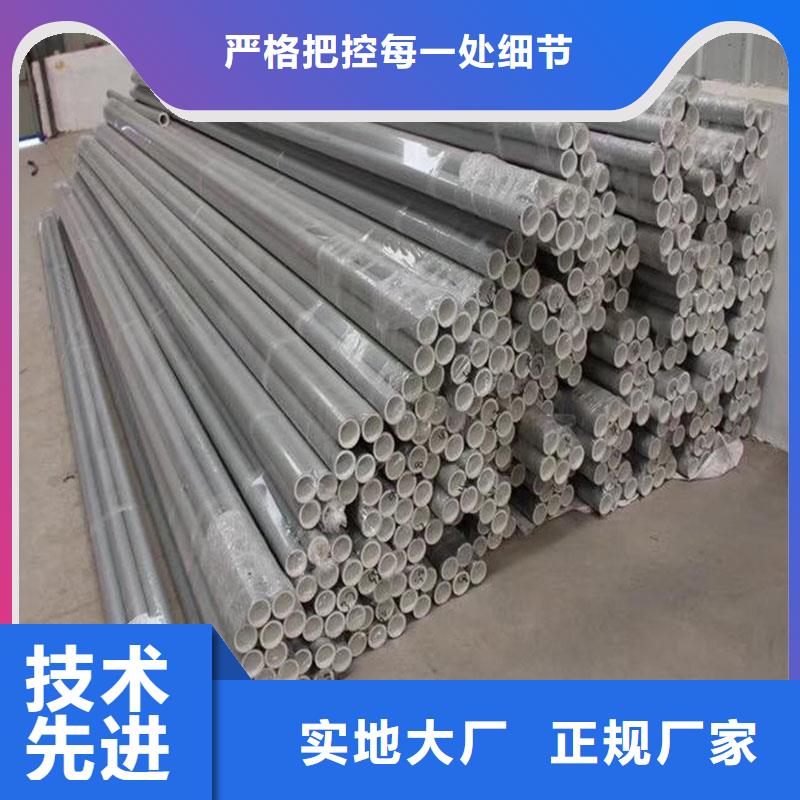
对于门窗幕墙型材,有质量缺陷隐患的主要在以下几点:(1)主要受力杆件;(2)产品结构和组装连接方式;(3)防护技术方案;对照铝合金门窗、幕墙的设计规范,确认受力杆件的技术参数(壁厚与力学性能),对照节点图,确认结构和连接方式,关注门窗幕墙可能出现高空坠落隐患的结构件,重点在于与铝合金产品相关的力学性能、特征值、表面处理(贴玻璃面)等参数确认。对于工业型材,铝制品的应用范围扩大,我们需要了解出厂产品的后续加工、应用场景、技术要求等更多的息,特别是对以下产品需要慎重:(1)特定、特殊用途的铝型材。例如航空航天专用材料、轨道交通、汽车轻量化、卫生医疗等有特定要求的应用领域;(2)需要签订质量缺陷、法律责任并涉及赔偿额度大的铝型材合同。例如重点公司(军工企业)、重点项目(超高层建筑、特殊区域工程项目)等;(3)发往欧盟、美国、日本等发达 的工业产品。例如环保、产品标识、防护申明等,业内有企业莫名其妙成被告的情况。2.质量缺陷过程管控--从管理角度,依靠管理体系是根本解决办法。对于铝行业而言,部分企业管理体系有效性一般,依靠日常管控系数较低,需要有针对性的重点管理,建议如下:(1)建立《内部质量缺陷清单》。一份常规清单,针对产品的性能指标;一份临时清单,特定项目。清单仅仅用于内部管控,严禁外发。(2)重要参数监控分析。如有可能,建议用控制图。(3)提高检验频次,增加后续监督抽查,并严格管理检测记录。(4)明确并落实各环节人员责任。记得十多年前,做新加坡地铁工程项目,客户跟各工序人员见面并合影拍照,然后告诉我们,照片会对应姓名、职位、负责环节等息一起存档备案,新加坡 会感谢我们为合格产品付出了努力,如果因产品质量缺陷而造成不利影响,存档息将作为追责的依据。灌输、强调质量意识是对的,关键时候“责任到人”产生的威慑力效果 。3.售后服务及应急预案--受制于企业管理的流程和文化,售后服务容易出现推诿扯皮、拖延搪塞,回复和跟进处理速度相对偏慢,建议针对质量缺陷建立相应的内部应急预案。近日网上未经确认的消息:特斯拉被德国一家租赁公司取消了85辆Model 3的订单,退订金额高达500万欧元,理由是特斯拉之前交付的15辆汽车存在严重质量问题。该公司公开表示,特斯拉的出现的问题众多,包括轮胎、油漆和车身损坏,充电控制器缺陷、线路故障、紧急呼叫按钮丢失等问题。发现质量缺陷,快速反应,组建专业团队协商出解决方案,避免更大损失才是上策。在息数据高速发展的今天,回避问题,漠视质量缺陷, 是不明智的!五、质量瑕疵的控制:相对于缺陷而言,瑕疵的话题没那么恐怖,从问题严重性上分析,缺陷的后果是巨额赔偿,甚至直接责任人要受到法律制裁,对企业和个人都是无法承重的打击。瑕疵毕竟属于技术和经济范畴,能通过商业行为找到解决方案。1.可量化质量参数:出于好奇心,我选取部分铝型材企业做过过程能力指数测试,抽取样品中有业内公认质量 梯队,也有中小型企业,*终结果比想象的差,数据统计显示,结果跟性能参数关联度高,跟企业关联度低,为避免争议,只公布各性能参数的过程能力范围,以便大家可以找到管控重点。化学成分:达到Ⅱ级及以上,过程能力充分,技术管理能力很好;力学性能:达到Ⅲ级及以上,过程能力充分,技术管理能力较勉强;几何尺寸:达到Ⅳ级及以下,过程能力不足,技术管理能力很差;涂层厚度:达到Ⅲ级及以上,过程能力充分,技术管理能力较勉强;室温抗剪特征值:达到Ⅲ级及以上,过程能力充分,技术管理能力较勉强;高温抗剪特征值:达到Ⅳ级及以下,过程能力不足,技术管理能力很差。其他指标抽取的企业样品数较少,不能妄下结论。通过上述结果可以看出,困扰从业人员的根本问题在于过程能力指数偏低,过程波动带来的直接后果是不合格品出现的概率偏高,只能用后续检验做补救,这种管理属于“亡羊补牢”式,让大家陷入不合格品的汪洋大海中不能自拔,成为常态,也是很多企业管理人员痛苦的根源!过程能力指数与标准偏差和允许公差范围有关,前者重点在于“人、机、料、法、环、测”的持续改进,后者在于与客户的沟通协商,二者都是过程能力指数变化的重要因素。2.不可量化质量问题:表面质量问题,是质量瑕疵被投诉的重灾区,无法量化,也很难形成统一的标准,产生很多质量异议,销售、生产、质量、加工厂、客户之间,处于一种动态博弈形态,某一阶段可以达成产品标准,随时会因为某一模块出现变化,形成新的异议,处于“异议→投诉→协商→标准→异议”的循环之中。感性认识指标具有一定的灵活性,需要专业技术人员和销售团队集体攻关。对内,加强细节管控,对外,与客户积极沟通,了解客户抱怨的真实原因和期望,有针对性解决问题。3.关于质量瑕疵的总结:(1)所有的工业产品都可以找到瑕疵,铝型材产品更加容易找到,面对问题先有足够的心理承受能力,才有解决问题的思路;(2)所有客户都是可以沟通的,关键是沟通的人和方法,遇到阻力,需要综合分析多层次的原因;(3)质量瑕疵的成本不能高于过程制造成本,企业不是科研单位,解决问题的管理方案是受成本限制的;(4)企业发展战略很重要,产品质量瑕疵的和处理是为企业战略服务的;(5)质量瑕疵有很强的时效性,不同阶段客户的关注点是会发生变化。六、结束语:经过四十多年的推广和宣传,中国的质量管理进入一个相对成熟的阶段,产品质量有了大幅度的提高,市场也是与时俱进,对于产品质量有更高的预期。铝加工产品也是如此。持续改进成为质量的永恒主题。明确质量缺陷和质量瑕疵的分类,坚决防止有缺陷的产品出厂,严格控制有瑕疵的产品流入敏感客户手中,是铝加工质量管理重点。企业经营看结果,结果源于过程。认真研究过程中的相关要素,分别给与适当的关注和管控,才是解决问题的根本。小技巧改变的是局部,大智慧决定的是根基,只有踏踏实实做好现场基础工作,才能从根本上扭转铝型材行业质量管理现状。
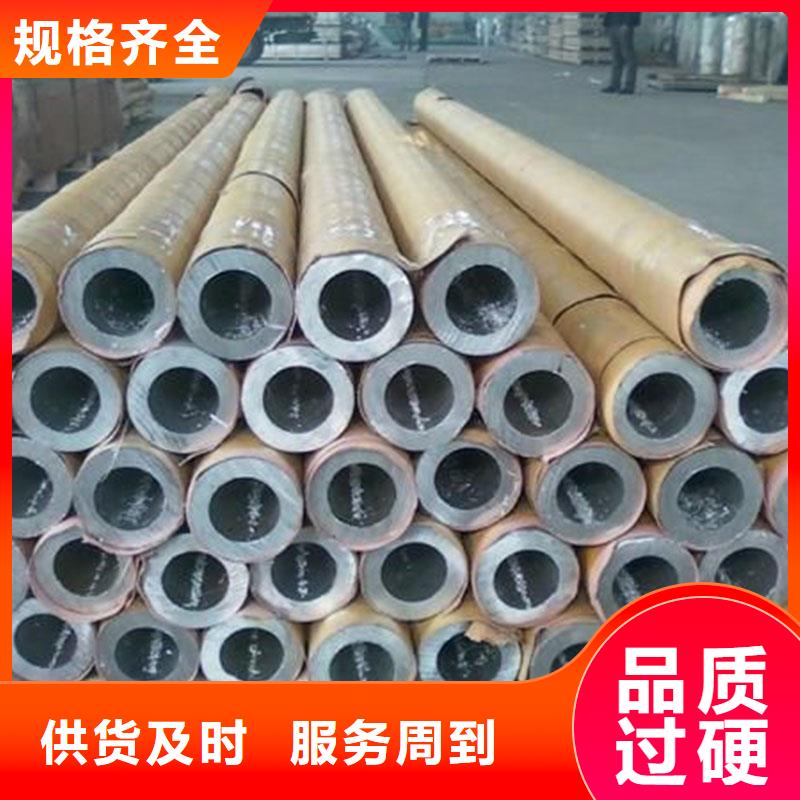
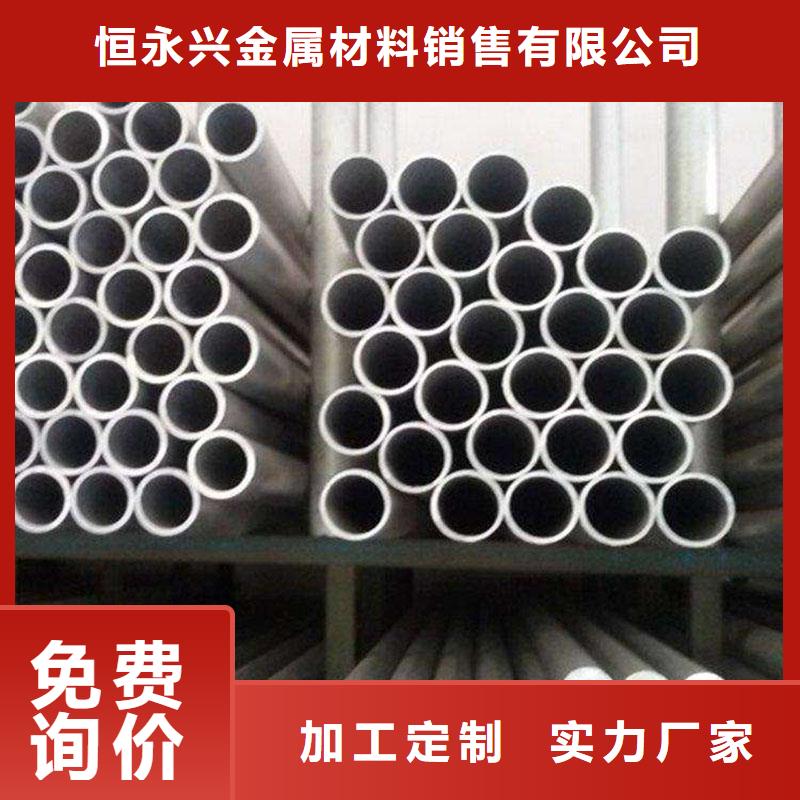
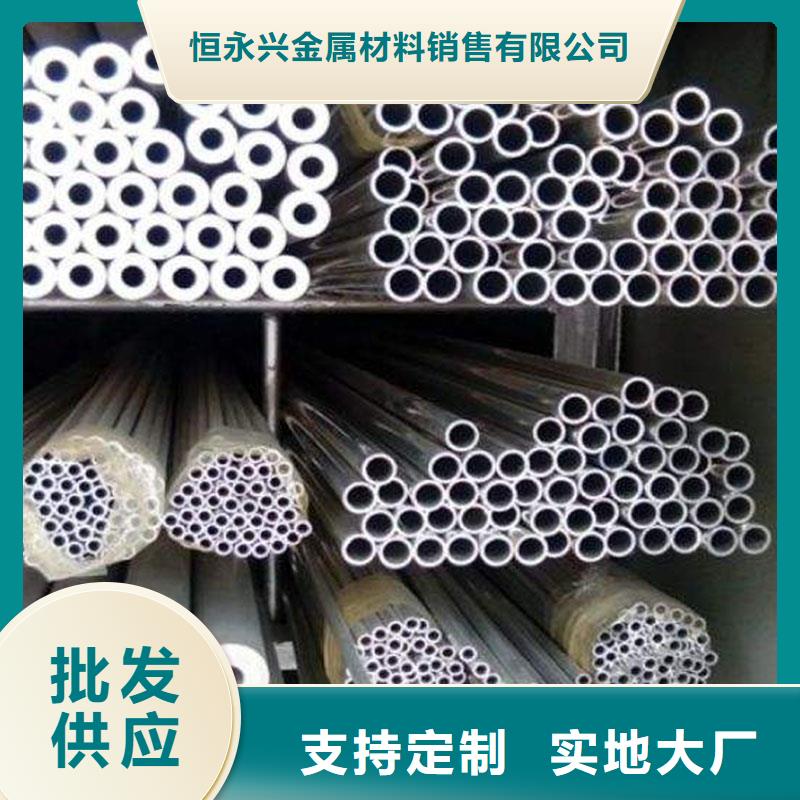
铝及铝合金焊丝的选择主要根据母材的种类,对接头抗裂性能、力学性能及耐蚀性等方面的要求综合考虑。有时当某项成为主要矛盾时,则选择焊丝就着重从解决这个主要矛盾入手,兼顾其它方面要求。一般情况下,焊接铝及铝合金都采用与母材成分相同或相近牌号的焊丝,这样可以获得较好的耐蚀性;但焊接热裂倾向大的热处理强化铝合金时,选择焊丝主要从解决抗裂性入手,这时焊丝的成分与母材的差别就很大。
常见缺陷(焊接问题)及防止措施1、烧穿---产生原因:a、热输入量过大;b、坡口加工不当,焊件装配间隙过大;c、点固焊时焊点间距过大,焊接过程中产生较大的变形量。防止措施:a、适当减小焊接电流、电弧电压,提高焊接速度;b、大钝边尺寸,减小根部间隙;c、适当减小点固焊时焊点间距。2、气孔---产生原因:a、母材或焊丝上有油、锈、污、垢等;b、焊接场地空气流动大,不利于气体保护;c、焊接电弧过长,降低气体保护效果;d、喷嘴与工件距离过大,气体保护效果降低;e、焊接参数选择不当;f、重复起弧处产生气孔;g、保护气体纯度低,气体保护效果差;h、周围环境空气湿度大。防止措施:a、焊前仔细清理焊丝、焊件表面的油、污、锈、垢和氧化膜,采用含脱氧剂较高的焊丝;b、合理选择焊接场所;c、适当减小电弧长度;d、保持喷嘴与焊件之间的合理距离范围;e、尽量选择较粗的焊丝,同时增加工件坡口的钝边厚度,一方面可以允许使用大电流,公众号:焊王,另一方面也使焊缝金属中焊丝比例下降,这对降低气孔率是行之有效的;f、尽量不要在同一部位重复起弧,需要重复起弧时要对起弧处进行打磨或刮除;一道焊缝一旦起弧要尽量焊长些,不要随意断弧,以减少接头量,在接头处需要有一定焊缝重叠区;g、换保护气体;h、检查气流大小;i、预热母材;j、检查是否有漏气现象和气管损坏现象;k、在空气湿度较低时焊接,或采用加热系统。3、电弧不稳---产生原因:电源线连接、污物或者有风。防止措施:a、检查所有导电部分并使表面保持清洁;b、将接头处的脏物掉;c、尽量不要在能引起气流紊乱的地方进行焊接。4、焊缝成型差---产生原因:a、焊接规范选择不当;b、焊枪角度不正确;c、焊工操作不熟练;d、导电嘴孔径太大;e、焊丝、焊件及保护气体中含有水分。防止措施:a、反复调试选择合适的焊接规范;b、保持合适的焊枪倾角;c、选择合适的导电嘴孔径;d、焊前仔细清理焊丝、焊件,保证气体的纯度。5、未焊透---产生原因:a、焊接速度过快,电弧过长;b、坡口加工不当,装备间隙过小;c、焊接规范过小;d、焊接电流不稳定。防止措施:a、适当减慢焊接速度,压低电弧;b、适当减小钝边或增加根部间隙;c、增加焊接电流及电弧电压,保证母材足够的热输入能量;d、增加稳压电源装置e、细焊丝有助于提高熔深,粗焊丝提高熔敷量,应酌情选择。6、未熔合---产生原因:a、焊接部位氧化膜或锈迹未干净;b、热输入不足。防止措施:a、焊前清理待焊处表面b、提高焊接电流、电弧电压,减小焊接速度;c、对于厚板采用U型接头,而一般不采用V型接头。7、裂纹---产生原因:a、结构设计不合理,焊缝过于集中,造成焊接接头拘束应力过大b、熔池过大、过热、合金元素烧损多;c、焊缝末端的弧坑冷却快;d、焊丝成分与母材不匹配;e、焊缝深宽比过大。防止措施:a、正确设计焊接结构,合理布置焊缝,使焊缝尽量避开应力集中区,合理选择焊接顺序;b、减小焊接电流或适当增加焊接速度;c、收弧操作要正确,加入引弧板或采用电流衰减装置填满弧坑;d、正确选用焊丝。8、夹渣---产生原因:a、焊前清理不彻底;b、焊接电流过大,导致导电嘴局部熔化混入熔池而形成夹渣c、焊接速度过快。防止措施:a、加强焊前清理工作,多道焊时,每焊完一道同样要进行焊缝清理;b、在保证熔透的情况下,适当减小焊接电流,大电流焊接时导电嘴不要压太低;c、适当降低焊接速度,采用含脱氧剂较高的焊丝,提高电弧电压。9、咬边---产生原因:a、焊接电流太大,焊接电压太高;b、焊接速度过快,填丝太少;c、焊枪摆动不均匀。防止措施:a、适当的调整焊接电流和电弧电压;b、适当增加送丝速度或降低焊接速度;c、力求焊枪摆动均匀。10、焊缝污染---产生原因:a、不适当的保护气体覆盖;b、焊丝不洁;c、母材不洁。防止措施:a、检查送气软管是否有泄漏情况,是否有抽风,气嘴是否松动,保护气体使用是否正确;b、是否正确的储存焊接材料;c、在使用其它的机械清理前,先将油和油脂类物质掉;d、在使用不锈钢刷之前将氧化物掉。11、送丝性不良---产生原因:A、导电嘴与焊丝打火;b、焊丝磨损、喷弧;d、送丝软管太长或太紧;e、送丝轮不适当或磨损;f、焊接材料表面毛刺、划伤、灰尘和污物较多。防止措施:a、降低送丝轮张力,使用慢启动系统;b、检查所有焊丝接触表面情况并尽量减少金属与金属的接触面;c、检查导电嘴情况及送丝软管情况,检查送丝轮状况;d、检查导电嘴的直径大小是否匹配;e、使用耐磨材料以避免送丝过程中发生截断情况;f、检查焊丝盘磨损状况;g、选择合适的送丝轮尺寸,形状及合适的表面情况;h、选择表面质量较好的焊接材料。12、起弧不良---产生原因:a、接地不良;b、导电嘴尺寸不对;c、没有保护气体。防止措施:a、检查所有接地情况是否良好,使用慢启动或热起弧方式以方便起弧;b、检查导电嘴内空是否被金属材料堵塞;c、使用气体预清理功能;d、改变焊接参数。
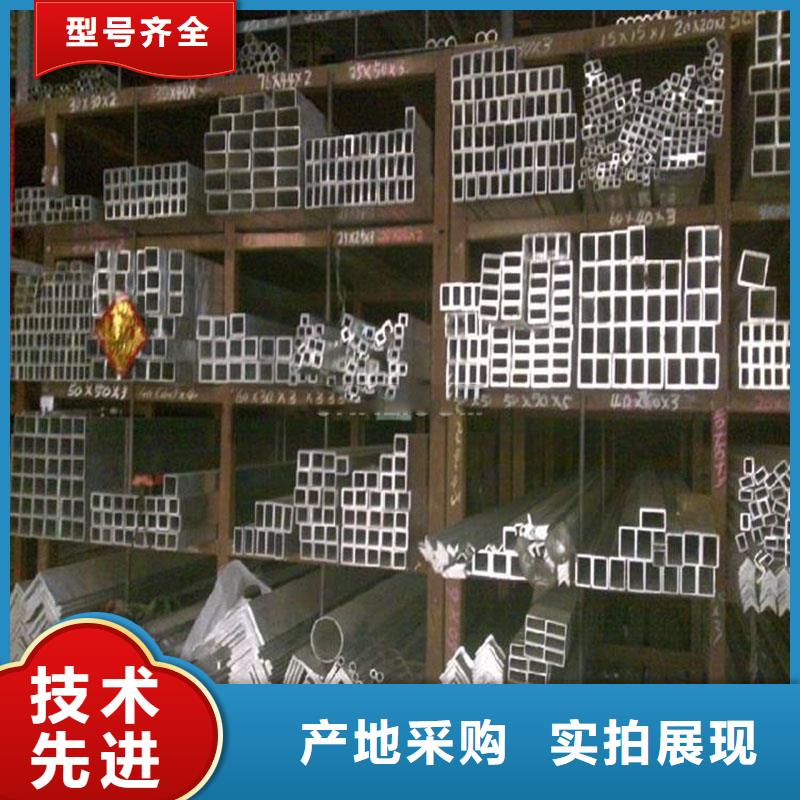

轮圈,是轮胎内廓支撑轮胎的圆桶形的、中心装在轴上的金属部件。二、按材质分类:轮圈按照材料主要分为铁轮圈和轻合金轮圈,而轻合金轮毂又以铝合金与镁合金产品为主。在今天的汽车市场中,铁制轮圈已不多见,大多数车型使用的都是铝合金轮圈,铝车轮。制造铝制轮圈所使用的铝合金材料包括A356、6061等。其中,A356被铸造铝制轮圈大量选用。A356铝合金具有比重小,耐侵蚀性好等特点,主要由铝、硅、镁、铁、锰、锌、铜、钛等金属元素组成,铝占92%左右,是一种技术成熟的铝合金材料。制造铝合金轮圈的原材料A356铝锭↑↑三、铝合金轮圈生产工艺:铝合金轮圈比钢轮圈更适合乘用车,目前其制造工艺基本可分为三种, 种是铸造,目前大多数汽车厂商都选择使用铸造工艺。第二种是锻造,多用于高端跑车、高性能车以及高端改装市场。第三种较为特别,是*先由日本Enkei公司投入使用的MAT旋压技术,目前此技术在国内的应用不如前两种多。1、重力铸造法:重力铸造简单的说,主要是靠铝水自身的重力来冲填铸模,是一种较为早期的铸造方法。该法成本低、工序简单且生产效率高,然而,浇注过程中夹杂物易卷入铸件,有时还会卷入气体,形成气孔缺陷。重力铸造生产的轮圈易产生缩孔缩松且内部质量较差,此外,铝液流动性的限制也有可能导致造型复杂的轮毂良品率低。因此,汽车轮圈制造业已经很少使用该工艺了。2、低压铸造法:低压铸造是铝液在压力作用下充入模具,在有压力的情况下进行凝固结晶的工艺。同样的情况下,与重力铸造相比,低压铸造轮毂内部组 织更为密实,强度更高。此外,低压铸造利用压力充型和补充,极大简化浇冒系统结构,使金属液收得率可达90%。目前低压铸造已成为铝轮圈生产的 工艺,国内多数铝合金轮圈制造企业都采用此工艺生产。但低压铸造法也有其缺点:铸造时间较长,加料、换模具耗时长,设备投资多等。 3、锻造法:热锻(Hot forging)→RM锻造(RM forging)→冷旋压(Cold spinning)→热处理(Heat treatment)→机加工(Machine work)→喷丸处理(Shot blast)→表面处理(Surface finishing)锻造是固体到固体的变化,通过拍、压、锻等手段来形成轮毂样式,这个过程不会发生液相变化,都是固体变化。所以它的力学性能比铸造要高,具有强度高、抗蚀性好、尺寸精 确等优点。晶粒流向与受力的方向一致,因此强度、韧性与疲劳强度均显着优于铸造铝轮圈。同时,锻造铝轮毂的典型伸长率为12%~17%,因而能很好的吸收道路的震动和应力。另外,锻造铝轮圈表面无气孔,因而具有很好的表面处理能力。但是,锻造铝轮圈的*大缺点是生产工序多,生产成本比铸造的高得多。虽然锻造轮圈的性能更好,但汽车厂商在大部分车辆上还是主要使用铸造轮圈,只有少部分豪华车配备锻造轮圈。不过国内轮圈制造龙头企业中戴卡已成功进入乘用车锻造轮圈生产线并将锻造轮圈的成本压缩到了千元,并已经开始作为原配轮圈供应国内合资厂。4、挤压铸造法:挤压铸造也称为液态模锻,是集铸造和锻造特点于一体的工艺方法——将一定量的金属液体直接浇入敞开的金属型内,通过冲头以一定的压力作用于液体金属上,使之充填、成形和结晶凝固,并在结晶过程中产生一定量的塑性变形。优点:充型平稳,金属直接在压力下结晶凝固,所以铸件不会产生气孔、缩孔和缩松等铸造缺陷,且组 织致密,机械性能比低压铸造件高且投资大大低于低压铸造法。缺点:与传统锻造产品一样,需要铣削加工来完成轮辐的造型。日本已有相当部分的汽车铝轮毂采用挤压铸造工艺生产,从浇注金属液到取出铸件整个过程都由计算机来控制,自动化程度非常高。目前世界各国都把挤压铸造作为汽车铝轮圈生产的方向之一。5、特种成型:旋压技术:旋压技术*先在日本投入使用,严格而言还应算是铸造中的一种,指的是在轮圈整体铸造出型后再利用专用设备对受力处进行旋转加压处理,使得被处理位置金属内部分子排列发生改变,具体的分割面相比起一般铸造产品呈现密度更高的纤维状,从而改变整体金属力学的工艺方法。旋压技术制造的轮圈的质量、强度、延伸性等特性都已接近于锻造轮圈,且现对于锻造轮圈来说,更易生产。总的来说,MAT旋压技术既可相对保证轮毂制造成本,同时还可使铸造轮圈打造出与锻造轮圈相近的重量和强度。只是国内技术不成熟,成本较高,故应用不多。
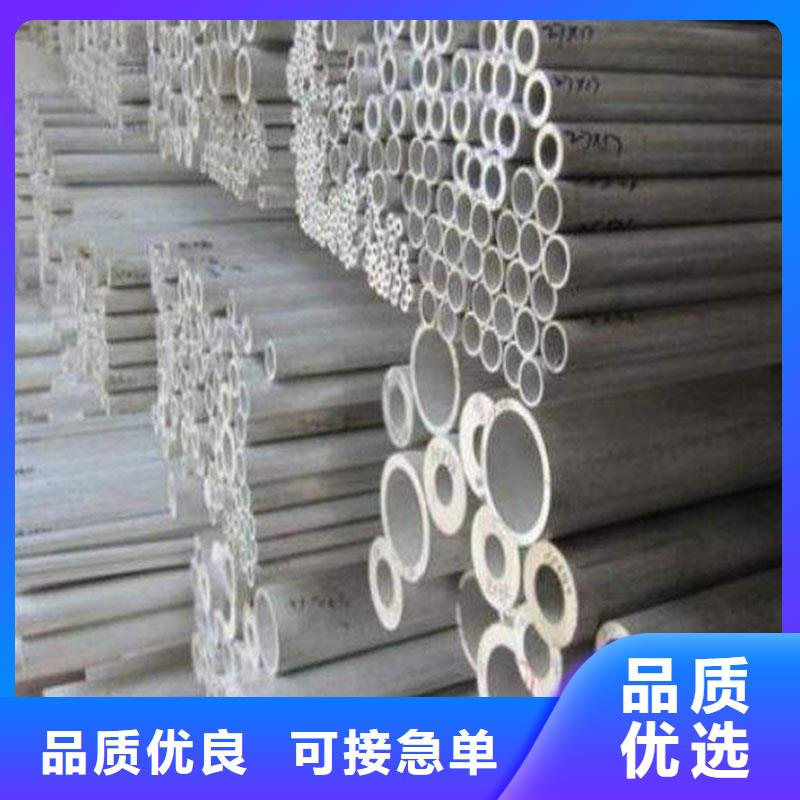
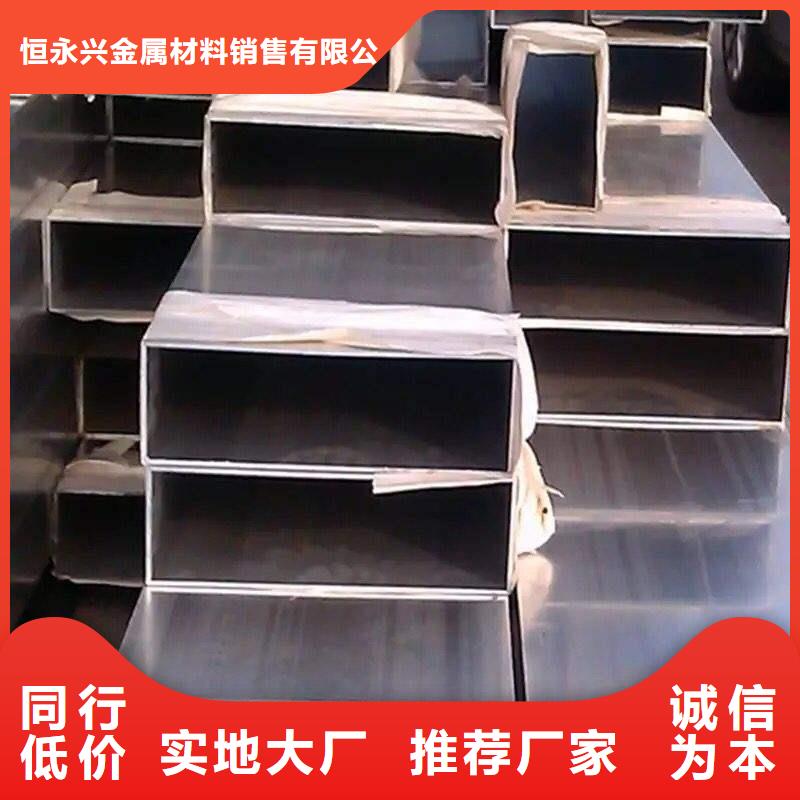

浅谈如何提高铝型材用粉末涂料的耐候性:喷涂在铝型材表面的粉末涂膜的耐候性,是影响铝型材寿命的关键性因素。本文主要从粉末涂料的原材料、配方结构、制作工艺、固化条件等技术角度分析,并结合所做的实验结果,总结出几个提高粉末涂料耐候性的可供参考的思路,从而*终达到延长铝型材寿命的目的。随着国民经济的快速发展,粉末涂料的户外应用越来越普遍,人们对粉末涂层耐候性和耐久性的关注度不断提高,特别是对铝型材、天花板、幕墙板等室外用品表面的粉末涂膜的耐候性要求越来越高。粉末涂料主要由树脂、固化剂、助剂、颜填料等组成,喷涂在铝型材表面的涂层随着时间的延长,受周围自然因素如日晒、雨淋、氧化、冷热变化以及生物等的作用,会出现性能逐渐降低的现象,即老化。粉末涂料抑制或延缓自然老化的能力称为耐自然老化性,简称耐老化性,也叫耐候性。影响粉末涂料耐候性的因素很多,其中包括粉末涂料成分中的树脂、固化剂、颜填料、助剂等各种原材料的性能、用量、配比等内部因素;以及粉末涂料制作过程的工艺条件和涂料的固化程度;还有涂膜的使用环境如日光(主要是紫外线)的作用、大气的组成(氧、臭氧、工业烟雾等)、湿度(包括酸雨、盐雾等)、温度变化等外部因素。
从粉末涂料本身的角度来看,提高粉末涂层耐候性能主要从原材料、配方结构以及制作工艺等方面着手。一、原材料:粉末涂料主要由树脂、固化剂、助剂、颜填料等材料组成,这些原材料的耐候性,基本上决定了涂料的耐候性。因此,要提高粉末涂料的耐候性能,首先要选择耐候性能满足铝型材行业要求的原材料,而且这些耐候性合格的原材料也要满足涂膜的其他性能。当涂膜的各项性能相互间产生冲突时,可以根据客户的要求侧重于某项性能,但是人工加速老化试验结果要满足GB 5237.4-2008中加速耐候性的要求。1.树脂:因为树脂是粉末涂料的主要成膜物质,是决定粉末涂料性质和涂膜性能的*主要成分,所以树脂的选择至关重要。选取市面上大型厂家常用的铝型材用粉末涂料聚酯树脂,使用同一配方结构和相同制作工艺分别制粉进行300小时耐老化试验以及涂膜外观比较,结果如表1所示。(加速老化条件为8小时光照,4小时凝露循环;UVB-313EL灯,辐照度0.65W/㎡,光照温度60℃;凝露温度50℃)由试验结果可知,树脂D、F、H在通一系列的树脂中耐候性较好,但这种树脂的缺点是分子量大,熔融黏度高,如果应用在平面粉中*终会导致涂膜流平性能差。所以,通过在粉末涂料配方中选用耐候性能好的树脂来提高平面粉的耐候性能时,必须考虑到涂膜的流平是否会变差,变差之后客户能否接受。2.固化剂:尽管HAA体系的固化剂环保型众所周知,但是它的缺点是固化反应有副产物形成,厚喷时容易产生针孔、猪毛孔等弊端,涂膜过烘烤耐泛黄性和耐久性不如TGIC体系。[1]铝型材行业目前难以接受HAA体系的这些弊端,或者说是大部分粉末厂家没有解决这些弊端,所以铝型材用粉末涂料还是以TGIC体系为主。固化剂TGIC对粉末涂料的耐候性能也有一定的影响。
经过对国内三家销售量排名靠前的厂家的TGIC进行耐老化检测,发现它们的耐老化性能基本一致,无较大的差别。因此,在通过固化剂TGIC的选择上去提高粉末涂料的耐候性,并无多大的意义。3.颜料:颜料对粉末涂料耐候性的影响在原材料中是除了树脂之外影响*大的因素,因为颜料在使用过程中会褪色,所以对于铝型材用粉末涂料的颜料的选择也很重要。市场上即使是用一种颜色的颜料,它的品种非常多,不同品种的色相、着色力、遮盖力、耐候性、耐热性等性能千差万别,这给我们粉末涂料厂家的选择带来很大的难度。颜料按化学组成分为无机颜料和有机颜料,它们的优缺点如表2所示。颜料的选择要从多方面考虑,如颜料的色相、着色力、遮盖力、耐热性、耐候耐光性、耐沸水性、毒性等等;而且由于一些颜料可能带有对树脂和固化剂起到促进作用的活性基团,所以也要考虑颜料对涂料反应速度、粘度的影响。为了提高粉末涂料的耐候性,颜料要选择耐光性在7-8级(8级*好),耐候性4-5级(5级*好)的品种,同时耐热性和耐沸水性要满足铝型材行业的使用要求。从表2可知,由颜料本身的性质决定,有机颜料的耐光性和耐候性有限,而无机颜料不够鲜艳,所以一些鲜艳颜色的粉末大多使用了耐光性和耐候性有限的有机鲜艳颜料,这就是鲜艳颜色的涂膜耐老化色差较大的主要原因。因此,为了保证鲜艳颜色涂膜的耐候性,除了选用耐候性能优异的其他材料,更加要注意颜料的选择。4.填料:填料的重要功能是添加到粉末涂料中以后,能够改进涂膜的硬度、刚性和耐划伤性等物理力学性能,同时有利于改进粉末涂料的贮存稳定性、松散性和带电等性能。[3]铝型材粉末涂料中*常用的填料为硫酸钡,经过对多个厂家的硫酸钡进行耐老化检测,发现耐候性能无明显差别。因此,为了保证涂料的耐候性,必须使用纯度高的硫酸钡作为填料。硫酸钡进仓前必须经过检验,使用10%的盐酸溶液是*简单快捷的方法,可以快速检测出硫酸是否含有碳酸钙,碳酸钙会降低涂料的耐候性能,不能作为铝型材用粉末涂料的填料。5.助剂:在粉末涂料配方中,助剂的用量很少,但在一般粉末涂料配方组成中是不可缺少的成分,而且对涂膜的外观及某些性能起决定性作用。经过对各国内大型厂家同类助剂进行加速老化对比试验后,发现不同厂家的流平剂、光亮剂、安息香等对涂膜耐老化性能影响不大;而不同厂家的蜡粉、消光剂对涂膜耐老化的影响较大。因此,为了提高粉末涂料的耐候性,可以考虑使用耐老化性能好的蜡粉和消光剂。二、配方结构:通过粉末涂料中聚酯树脂的酸值和固化剂羟基当量的计算,设计合适的固化剂用量,并通过加速老化试验的验证,使用*佳的固化剂用量,使涂料在固化时能够充分固化,从而达到*好的耐候性能。
在满足粉末涂料各项性能的前提下,尽量在配方中减少原材料的种类,特别是对涂膜耐候性起负作用的材料。在不影响涂膜遮盖力以及硬度、耐磨性的前提下,适当降低配方中的颜料(特别是吸油量大的颜料)和填料的用量,使配方中的颜料能够在熔融混炼过程充分被树脂包覆,在涂膜的使用过程中减少颜料的颜色变化,从而达到提高涂膜耐候性的目的。三、制作工艺:粉末涂料制作过程主要包括预混合、熔融挤出、压片破碎、分级粉碎四个阶段,其中预混合、熔融挤出两个工艺对粉末涂料的耐候性能有很大影响。预混合的作用是为了使粉末涂料配方中的各种原材料组成分散均匀,为熔融挤出打下良好的基础。为了提高耐候性,在预混合阶段,原材料必须按一定的先后顺序进行投料,而且投料量控制在混料缸容量的20%-80%,并适当延长混合时间。熔融挤出是为了使粉末涂料组成中的各种成分混合均匀,也就是达到粉末涂料成品中的每个粒子组成成分一样。为了提高耐候性,在熔融挤出阶段,在不出现胶化粒子的前提下,适当提高挤出机温度(特别是在气温较低的情况下),使树脂熔融成一种流体,保证颜料能有良好的润湿和获得*大的剪切力,有利于颜料等的高度分散,使各组分成为一个均匀的体系;在保证生产进度的同时,可以适当降低挤出速度,保证物料有充足的熔融混炼时间;从而提高混炼效果,使粉末涂料中的颜料填料被树脂充分包覆,而且各种原材料成分粒子分散均匀,特别是固化剂和树脂能按配方的比例混炼均匀,固化时涂膜能够充分固化,从而增加涂膜的表面致密性,*终提高粉末涂层的耐候性。四、固化条件:粉末涂料只有充分固化的情况下,树脂的高分子链才会和固化剂完全交联,各项物理化学性能才会达到*佳状态,耐候性能也不例外。因此,提高耐候性能必须使粉末涂料充分固化,固化时要控制好温度和时间。综上所述,对于提高铝型材用粉末涂料的耐候性,可参考如下思路:选用耐候性能好且流平不至于太差的树脂;注意鲜艳颜料、蜡粉、消光剂的选择;设计有利于提高涂膜耐候性的配方结构;控制好粉末涂料生产工艺。
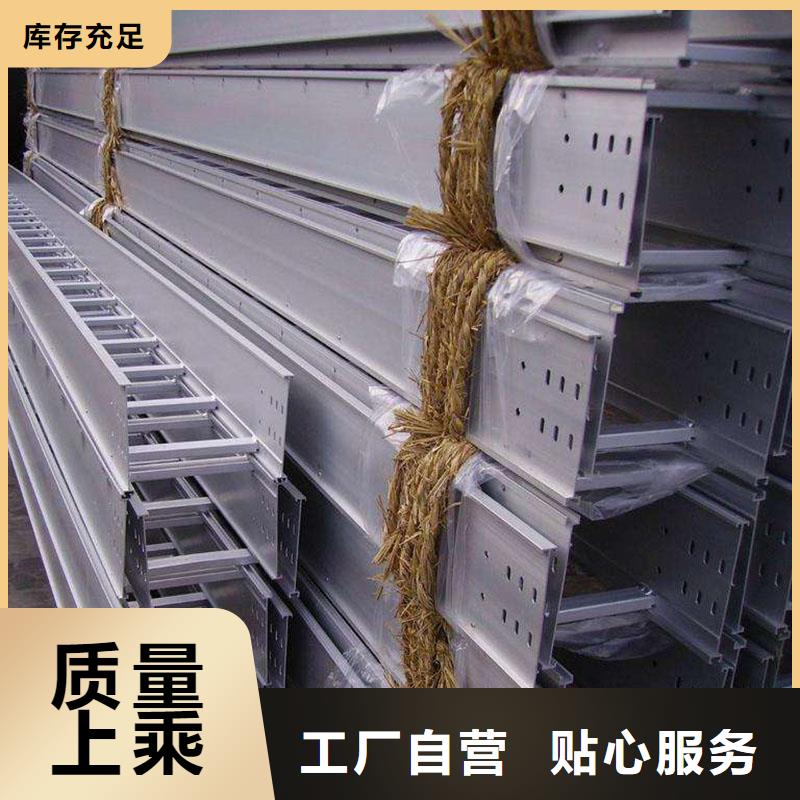
铝合金型材【镀锌工角槽】研发生产销售_恒永兴金属材料销售
有限公司,固定电话:18802286588,移动电话:022-86869388,联系人:李经理,QQ:554918566,北辰区双街镇京津路西(北方实业发展有限公司内) 发货到 湖北省黄石市。